Injection Molding Factories: The Backbone of Modern Manufacturing
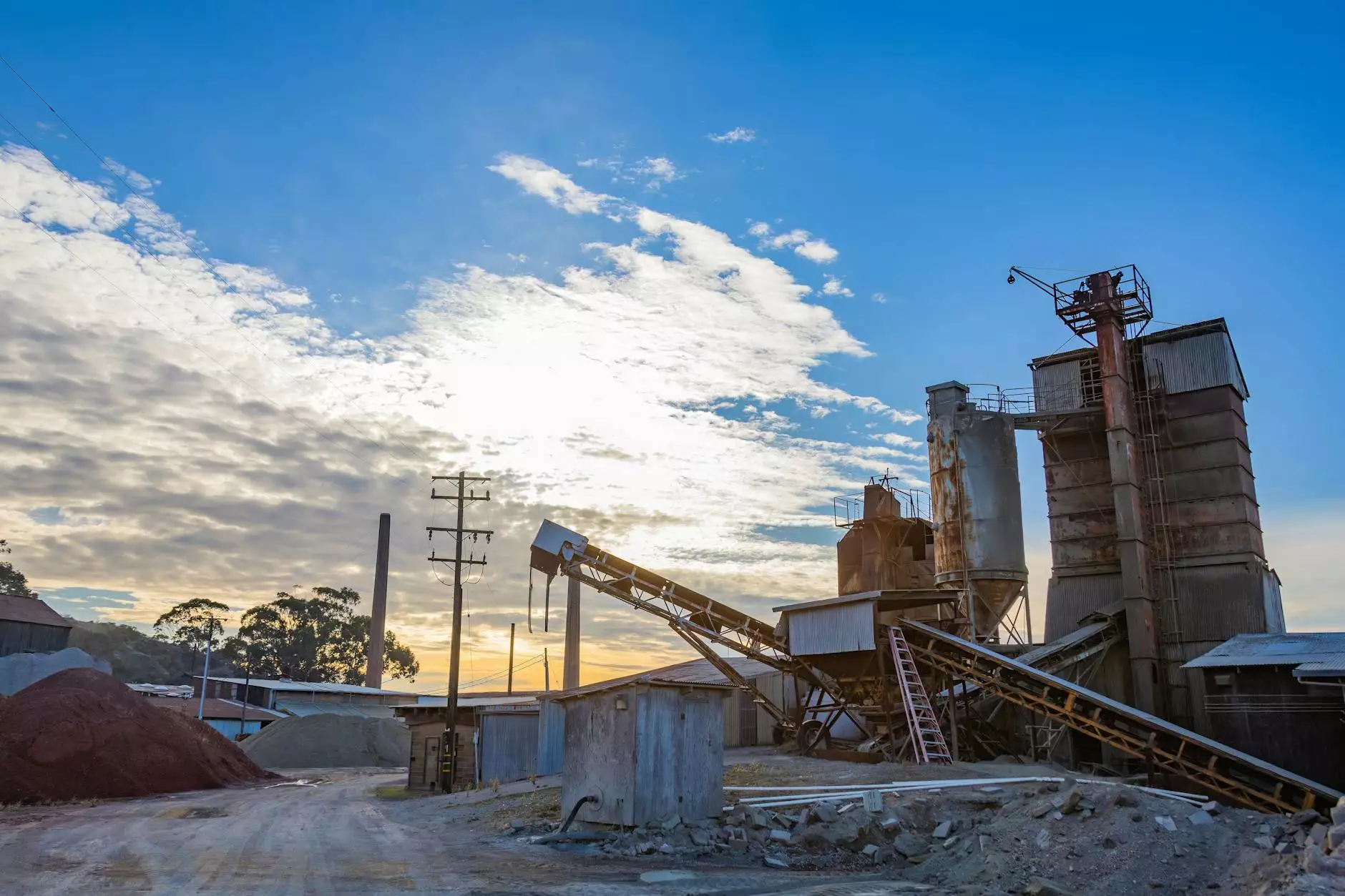
In an era where efficiency and precision are paramount, injection molding factories have emerged as a critical component of the manufacturing realm. These facilities not only epitomize advanced technology but also represent the core of productivity and creativity in various industrial sectors. This article delves into the intricacies of injection molding, shedding light on the processes, benefits, and future trends that define this fascinating field.
Understanding Injection Molding
At its core, injection molding is a manufacturing process used for producing parts by injecting molten material into a mold. The materials are typically plastics, but other substances such as metals and glass can also be molded. This method is celebrated for its ability to produce large volumes of parts with high precision, making it a popular choice in a myriad of industries.
How Injection Molding Works
The process of injection molding consists of several stages, each crucial to creating high-quality components:
- Material Selection: The first step involves choosing the right thermoplastic or thermosetting polymer that suits the intended application.
- Heating and Melting: The selected material is fed into a heated barrel where it melts into a viscous state.
- Injection: The molten material is then injected under high pressure into a mold cavity, ensuring every detail is captured.
- Cooling: Once the mold is filled, the material is allowed to cool and solidify, forming the desired shape.
- Demolding: Finally, the mold opens, and the finished part is ejected.
The Advantages of Injection Molding
Injection molding factories offer numerous advantages that make them an ideal solution for manufacturers:
- High Efficiency: Once the mold is set, injection molding can produce thousands of parts per hour.
- Precision and Repeatability: The process ensures consistent quality and dimensional accuracy across large production runs.
- Material Versatility: A wide range of materials, including various plastics and metals, can be used.
- Reduced Waste: The process is designed to minimize material waste, making it a more sustainable option.
Comparative Benefits Over Other Manufacturing Methods
When comparing injection molding factories with other manufacturing methods like CNC machining or 3D printing, several distinctions arise:
- Cost-Effectiveness: For high-volume production, injection molding often proves more cost-effective compared to other methods.
- Complex Shape Capabilities: It allows for greater complexity in design, including intricate details that may be challenging with machining.
Applications of Injection Molding
Injection molding is ubiquitous across various industries:
- Automotive: Parts such as dashboards, covers, and interior components are efficiently produced.
- Consumer Electronics: Many devices use injection-molded parts for housings and internal components.
- Medical Devices: Precision-molded parts are essential for the production of syringes, connectors, and other critical medical devices.
- Packaging: Injection molding is widely used in creating containers, bottles, and caps.
Future Trends in Injection Molding
The world of injection molding factories is constantly evolving. Innovations in technology and materials are shaping the future of this manufacturing process:
Advancements in Technology
With the rise of Industry 4.0, injection molding is becoming more automated and interconnected. Some notable trends include:
- IoT Integration: Smart sensors and connected machines are enabling real-time monitoring and predictive maintenance.
- Automation: Robotic arms and automated sorting systems are streamlining production processes.
- Sustainable Practices: A growing emphasis on recycling and the use of biodegradable plastics is transforming the industry.
The Role of DeepMould.net in Injection Molding
As a leading entity in the field, DeepMould.net exemplifies excellence in injection molding. Specializing in metal fabricators, DeepMould acts as a bridge between innovative design and real-world application. Their state-of-the-art facilities and commitment to quality ensure that every product meets the highest standards.
Quality Assurance and Customer Focus
DeepMould's approach values customer satisfaction and quality assurance. Through meticulous quality control processes, they guarantee that the manufactured items not only meet client specifications but also comply with industry standards. This ethos positions them as a trusted partner in the injection molding sector.
Challenges Facing Injection Molding Factories
Despite the numerous advantages, there are challenges that injection molding factories must navigate:
- High Initial Costs: Setting up molds and machinery can require significant investment.
- Long Lead Times: Designing and producing molds can take time, particularly for complex parts.
- Material Limitations: While many materials are compatible, not all plastic types can be injection molded efficiently.
Strategies for Overcoming Challenges
To address these challenges, companies can:
- Invest in Design Optimization: Employing advanced design software can help streamline the mold creation process.
- Collaborate with Suppliers: Building partnerships with material suppliers can lead to better material options and cost savings.
Conclusion
Injection molding factories are indispensable in the modern manufacturing landscape. With their ability to produce high-quality parts efficiently, they serve various industries globally. As technology advances and sustainability becomes a focal point, the future of injection molding appears bright. Companies like DeepMould.net pave the way for innovation in metal fabricators, driving the industry forward. Through understanding this vital process, businesses can leverage its benefits to enhance production capabilities and meet evolving market demands.