The Comprehensive Guide to Injection Mold Tool Manufacturing
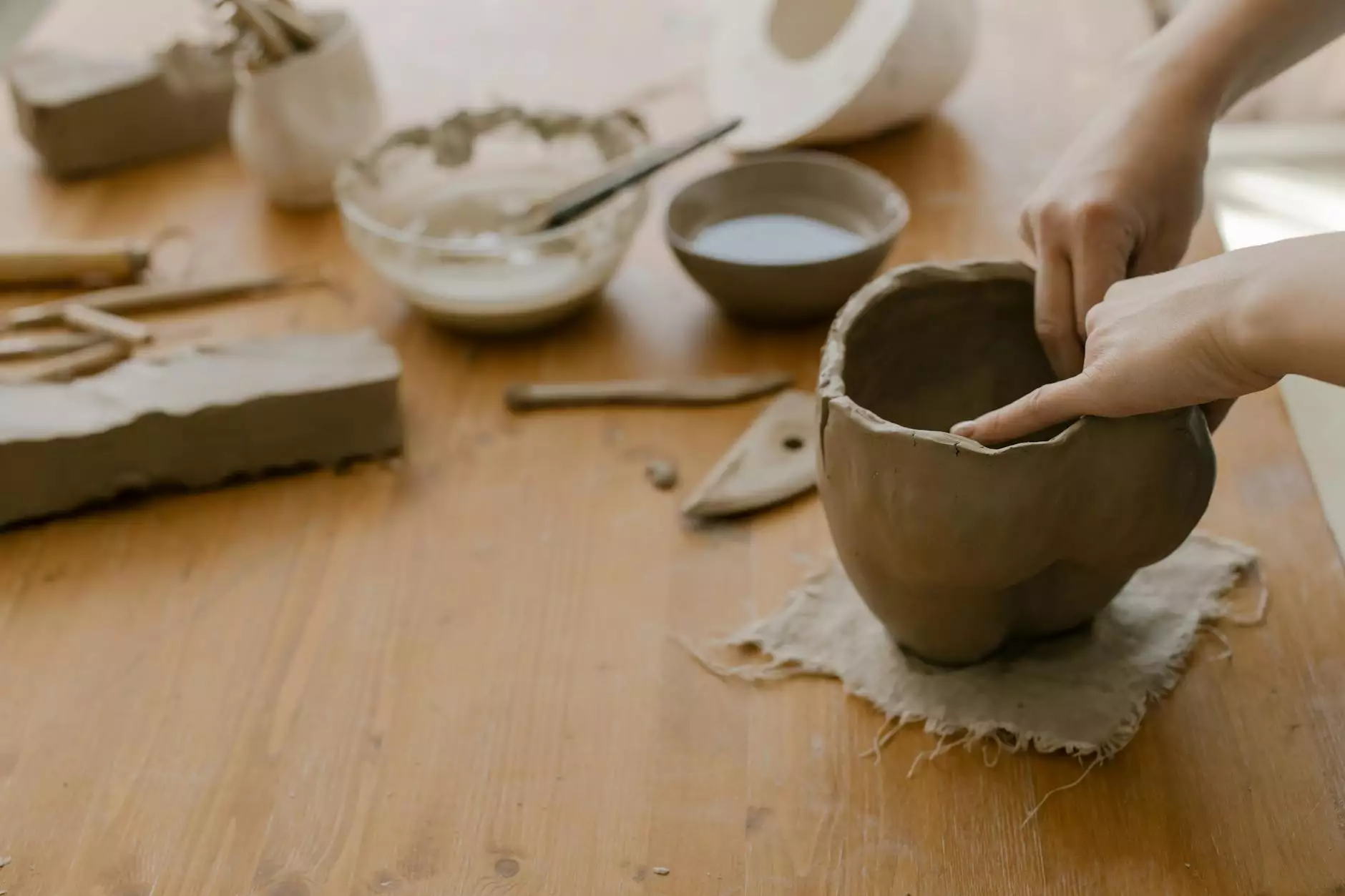
When it comes to precision manufacturing, few processes are as pivotal as the creation of the injection mold tool. The realm of metal fabricators relies heavily on this technology to produce high-quality parts consistently and efficiently. This article delves into the intricacies of injection mold tool manufacturing, its benefits, and how businesses can leverage it for superior outcomes.
What is an Injection Mold Tool?
The injection mold tool is a sophisticated piece of equipment used in the injection molding process. It serves as the blueprint for shaping plastic, metal, or other materials into desired forms. Designed with utmost precision, these tools dictate the quality, durability, and efficiency of the molded products.
Key Components of an Injection Mold Tool
- Core and Cavity: The two main components of the mold that define the shape of the final product.
- Gate: The entry point where the molten material enters the mold cavity.
- Ejector System: Mechanism that pushes the molded part out of the mold once it has cooled and solidified.
- Cooling Channels: Systems integrated into the mold to regulate temperature and speed up the cooling process of the injected material.
The Importance of Injection Mold Tools in Metal Fabrication
In the world of metal fabricators, the efficiency and quality of production are paramount. The injection mold tool is crucial in achieving these goals. Here’s why:
1. Enhanced Production Efficiency
Utilizing injection mold tools significantly decreases production times due to their ability to produce multiple parts simultaneously. This process maximizes output while minimizing operational costs.
2. Superior Quality Control
With precise engineering and design, injection mold tools ensure that each part produced meets stringent quality standards. This consistency builds trust with clients and reduces waste due to faulty parts.
3. Versatility in Design
Modern injection mold tools can accommodate a variety of designs, materials, and sizes, making them incredibly versatile. This adaptability is essential for metal fabricators looking to diversify their product offerings.
The Injection Molding Process: Step-by-Step
Understanding how an injection mold tool fits into the overall manufacturing process is vital. Here’s a breakdown of the injection molding process:
Step 1: Designing the Product
The process begins with a detailed design created using CAD (Computer-Aided Design) software. This design will inform the specifics of the injection mold tool necessary for production.
Step 2: Fabricating the Mold
Once the design is finalized, the next step is to fabricate the mold. This involves using materials like steel or aluminum and precise machining techniques to ensure the mold meets specifications.
Step 3: Setting Up the Injection Molding Machine
The mold is mounted onto the injection molding machine, where the injection molding cycle begins. The machine will heat the material until it becomes molten.
Step 4: Injecting the Material
After heating, the molten material is injected into the mold under high pressure, allowing it to fill the cavity completely.
Step 5: Cooling and Ejecting the Part
Once filled, the material cools and solidifies. The ejector system then activates, pushing the final product out of the mold. The part is now ready for inspection and further processing.
Advancements in Injection Mold Tool Technology
As the demand for fast, high-quality production increases, so too do the technological advancements in the realm of injection mold tools. Here are some trends shaping the industry:
1. Smart Manufacturing Integration
The incorporation of IoT (Internet of Things) into injection molding allows manufacturers to gather data in real-time, improving efficiency and enabling predictive maintenance of the tools.
2. 3D Printing Innovations
3D printing is becoming a viable option for rapid prototyping of mold designs, significantly reducing lead times in the development of new injection mold tools.
3. Improved Materials
Advancements in materials science have led to the development of stronger, more durable materials for molds, enhancing their lifespan and performance.
Challenges in Injection Mold Tool Manufacturing
While there are significant benefits to using injection mold tools, businesses must also navigate various challenges:
1. High Initial Costs
The upfront investment in designing and fabricating mold tools can be substantial, particularly for small businesses. However, these costs are often offset by the long-term savings achieved through efficient production.
2. Maintenance Requirements
Injection mold tools require regular maintenance to ensure they function optimally. Neglecting maintenance can lead to production delays and increased operational costs.
3. Design Limitations
Certain complex designs may be challenging to achieve with standard injection mold tools. This necessitates innovation in design and tooling approaches to meet specific client needs.
Best Practices for Successful Injection Mold Tool Usage
To maximize the benefits of an injection mold tool, consider the following best practices:
1. Invest in Quality Design
The design phase is critical; investing in high-quality design from the beginning will pay off in terms of efficiency and product quality.
2. Select the Right Materials
Choosing the appropriate material for both the mold and the products being created can significantly impact performance and longevity.
3. Regular Maintenance and Inspections
Establish a routine for inspecting and maintaining your injection mold tools to avoid unexpected downtimes and ensure consistent production runs.
4. Stay Informed on Industry Trends
Keep abreast of new technologies and trends in the injection molding industry; adapting to these changes can give your business a competitive edge.
Conclusion: The Future of Injection Mold Tools in Metal Fabricators
As we look ahead, the role of the injection mold tool in the metal fabricators industry is set to evolve. With advancements in technology, materials, and processes, businesses will have the opportunity to enhance efficiency and product quality like never before. By understanding and utilizing injection mold tools effectively, companies can position themselves for success in an increasingly competitive marketplace.
If you are ready to take your metal fabrication to the next level, partner with industry experts at deepmould.net to discover how our comprehensive solutions can streamline your operations and maximize your production potential.