The Importance of Plastic Moulding for Electrical Products in the Metal Fabrication Industry
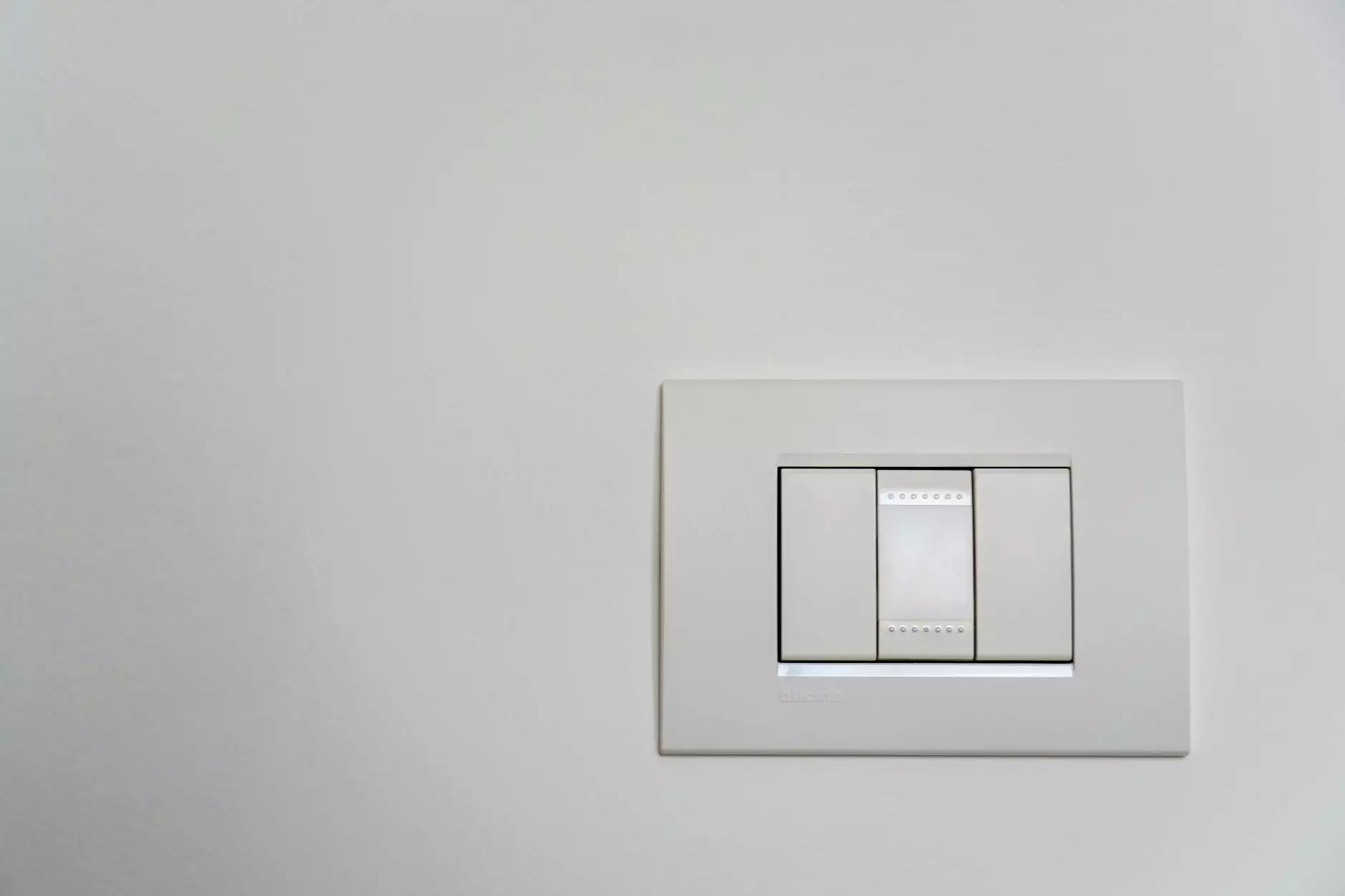
In the realm of Metal Fabricators, a crucial aspect that has significantly impacted the production of electrical products is plastic moulding for electrical. This innovative process has revolutionized the way electrical components are designed and manufactured, offering a plethora of benefits that enhance both functionality and efficiency.
Enhanced Precision and Customization
One of the key advantages of utilizing plastic moulding for electrical products is the ability to achieve unparalleled precision and customization. Manufacturers can create intricate designs and shapes that would be challenging or impossible to achieve by traditional methods. This level of precision ensures that the final products meet the exact specifications required for their intended applications.
Cost-Effectiveness and Efficiency
Plastic moulding for electrical products also offers a cost-effective solution for manufacturers. The process allows for high volumes of production at a relatively low cost per unit, making it an efficient choice for mass manufacturing. Additionally, the use of plastic materials can result in lighter components, reducing shipping costs and overall product expenses.
Durability and Longevity
With advancements in plastic materials and moulding technologies, electrical products manufactured using plastic moulding are known for their durability and longevity. These products can withstand harsh environmental conditions, resist corrosion, and provide excellent electrical insulation properties, ensuring a longer lifespan compared to traditional materials.
Environmental Sustainability
Plastic moulding for electrical products aligns with the growing emphasis on environmental sustainability in the manufacturing industry. By using recyclable and eco-friendly plastics in the production process, manufacturers can reduce their environmental impact and contribute to a more sustainable future. This move towards sustainability also resonates well with environmentally conscious consumers.
Innovation and Technological Advancements
The adoption of plastic moulding for electrical products has propelled innovation in the metal fabrication industry. Manufacturers are constantly exploring new materials, technologies, and design possibilities to push the boundaries of what is achievable in electrical product development. This culture of innovation drives continuous improvement and ensures that products remain at the forefront of technological advancements.
Conclusion
As the demand for high-quality, reliable electrical products continues to rise, the role of plastic moulding in the metal fabrication industry becomes increasingly vital. The benefits of precision, customization, cost-effectiveness, durability, sustainability, and innovation make plastic moulding a cornerstone of modern electrical product manufacturing. Deep Mould, as a leading provider of metal fabrication services, embraces these advancements to deliver exceptional solutions tailored to the evolving needs of the industry.